The Rise of Double Wall Coffee Cups A Dive into the Manufacturing Process
In recent years, the coffee culture has surged in popularity, with more people savoring their daily brews on the go. As a result, the demand for innovative and practical coffee accessories has increased. Among these innovations, double wall coffee cups have emerged as a favorite among consumers and manufacturers alike. This article delves into the significance of double wall coffee cups, the advantages they offer, and a peek into their manufacturing process.
Understanding Double Wall Technology
Double wall coffee cups feature an ingenious design consisting of two layers of material, typically glass or plastic, with a pocket of air in between. This innovative construction provides several key benefits. Firstly, it effectively insulates beverages, keeping hot drinks hotter for longer while ensuring the outer surface remains cool to the touch. This feature is particularly appealing to coffee enthusiasts who appreciate indulging in their favorite hot drinks without the risk of burning their hands.
Secondly, double wall technology significantly reduces the risk of condensation, which is a common issue with traditional cups. When iced beverages are served in standard cups, moisture tends to condense on the exterior, leading to a slippery and often messy experience. Double wall cups prevent this, providing a dry, comfortable grip for consumers.
The Manufacturing Process
The journey of a double wall coffee cup begins in the factory, where raw materials are sourced. Depending on the design, the materials could range from borosilicate glass for high-end models to durable BPA-free plastics for more affordable options. The choice of material not only affects the aesthetic appeal but also plays a crucial role in the cup’s insulation properties.
coffee cups double wall factory
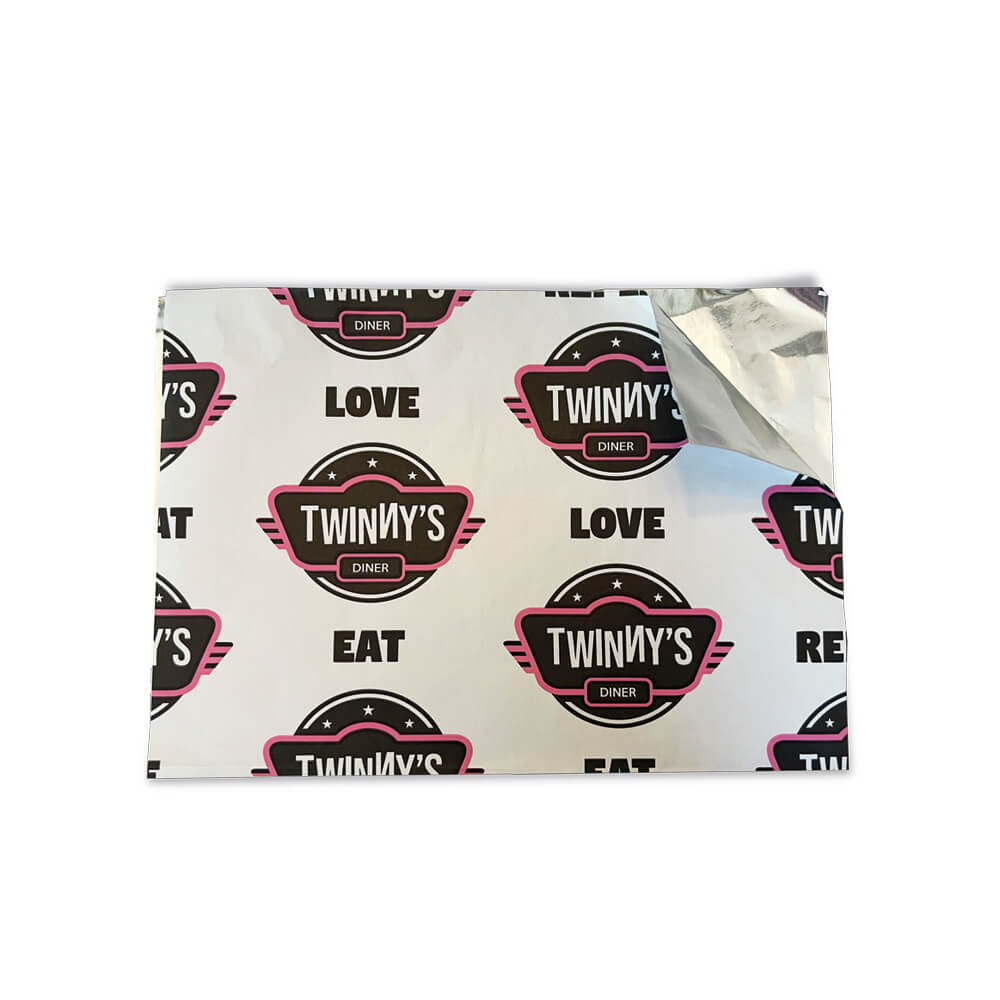
Once the materials are determined, the manufacturing process begins with the fabrication of the inner and outer walls. For glass cups, a glass-blowing technique is often employed, allowing skilled artisans to create the desired shapes and sizes. For plastic cups, injection molding is typically used, where molten plastic is injected into a mold to form the cup’s walls.
After the inner and outer layers are created, the assembly process involves fusing them together. This is a critical step; manufacturers must ensure the two layers are securely bonded to create the insulating air pocket. In some cases, manufacturers use specialized adhesives or even employ vacuum sealing techniques to enhance insulation and durability.
Once assembled, the cups undergo rigorous quality control checks. Each cup is inspected for any defects, such as uneven surfaces or weak bonds, as these imperfections can compromise functionality or safety. Only after passing these stringent checks can the cups move on to the decoration process, which may include printing logos, applying color coatings, or adding silicone grips for better handling.
Finally, the cups are packaged for distribution. Many manufacturers prioritize eco-friendly packaging solutions, reflecting growing consumer concerns over environmental impact. This commitment to sustainability aligns with the values of many coffee drinkers who consider their choices carefully, opting for products that minimize ecological footprints.
Conclusion
Double wall coffee cups exemplify the intersection of functionality and design within the coffee industry. As consumer preferences evolve, manufacturers respond by innovating and improving their product offerings. The journey from raw materials to finished product reveals not only the complexity of production but also the dedication of factories committed to quality craftsmanship. As coffee culture continues to thrive, the role of double wall coffee cups will undoubtedly remain significant, providing both comfort and convenience for coffee lovers worldwide.